

Success Stories

Manufacturing Scheduling
Process Improvement
Objective: Improve scheduling change and communications process
LEAN or DMAIC Tools used: Communications Spaghetti Diagram, Centralized “Real Time” SharePoint Scheduling Site for schedule updates
Results: Manufacturing schedule compliance improved from 84% to >90%
Injection Molding Tooling Maintenance
Objective: Change tooling maintenance approach from calendar-based to cycles-based approach
LEAN/DMAIC tools used: Tooling Durability Assessment at different machine cycles, Product Quality Architecture (Customer Requirements)
Results: Improved product quality; Reduced costs by $60,000 annually.
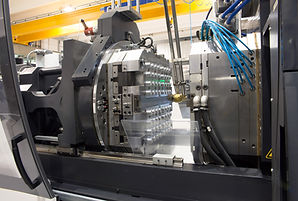
Manufacturing Production Lot Overrun
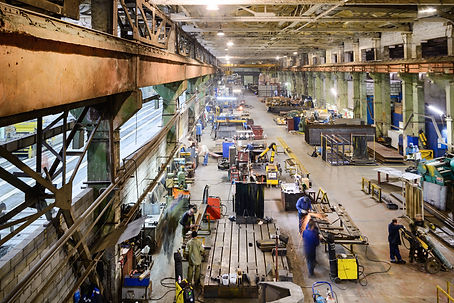
Objective: Reduce production of excess products before production job changes
LEAN/DMAIC tools used: Spaghetti diagrams (Molding area, Packing area), Visual Aids for Job changes (Electronic screen warnings for Mold and Packing areas), “Last count” factory communications notice
Results: Number of lots with proper products increased from 70% to over 90%. Scrap costs reduced by more than $70K.
Manufacturing Plant Redesign
Objective: To convert plant from primarily Ware-in-Process (WIP) manufacturing to a Raw Material to Finished Goods facility
LEAN/DMAIC tools used: Process Flow Diagrams, Inline volumetric measuring equipment development, Polarimeter assessment of glass sealing stress measurement
Results: Reduced Finished Goods manufacturing time from Forty-two days (42) to One day (1)
Reduced overall operating costs by > $1,000,000
​

Business IT Software Redesign
Objective: Reduce number of Business Software systems from Eight (8) to One (1)
LEAN/DMAIC Tools used: Process Flow Diagram, Process Simplification Assessment, Software Decision Analysis to identify new IT system
Results: Reduced IT staffing by Sixteen (16) FTE for a savings of over $800,000 annually.
​
